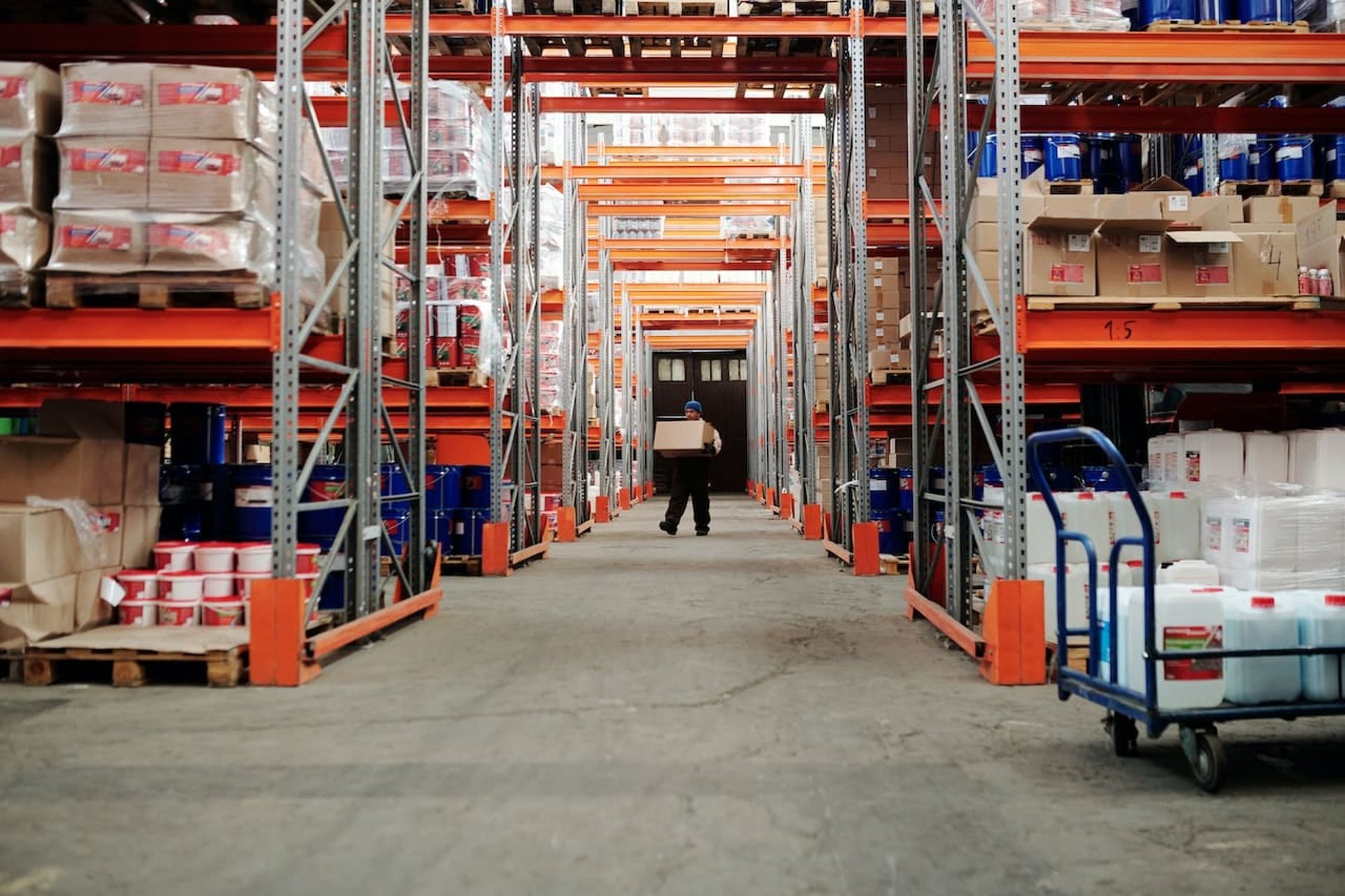
Un-Optimized inventory
Un-optimized inventory can be a significant challenge for businesses as it can lead to a number of problems such as:
Excess inventory: Carrying too much inventory can tie up capital and lead to higher storage and handling costs.
Stockouts: Running out of stock can lead to lost sales and damage to customer relationships.
Obsolescence: Carrying outdated or slow-moving inventory can lead to financial losses.
Inefficiency: Un-optimized inventory can lead to inefficiencies in production and distribution, resulting in higher costs.
To overcome these challenges, businesses can look for ways to optimize their inventory management. This can include:
Implementing an inventory management system: This can help businesses track inventory levels, set reorder points, and manage lead times more effectively.
Conducting regular inventory reviews: This can help businesses identify slow-moving or obsolete items, and make adjustments to their inventory accordingly.
Using inventory forecasting techniques: This can help businesses predict demand and plan inventory levels accordingly.
Implementing Just-In-Time (JIT) inventory: JIT inventory management system helps businesses to maintain a minimal level of inventory, which can reduce carrying costs and improve efficiency.
Implementing safety stock: This is a buffer stock held in inventory, to ensure that stockouts are avoided.
Incorporating supplier management: This can help businesses manage their inventory more effectively by working closely with suppliers to ensure timely delivery of goods.
Leveraging inventory optimization software: There are software available that can help companies to optimize inventory by analyzing data, predicting demand and identifying patterns.